【 IoT Core Connect, a platform service for utilizing Azure's IoT services | Case Study】
Introduced the “IoT Core Connect” platform service to revamp the remote monitoring service for turbo blowers. A mechanism to minimize equipment downtime was realized.
2022/09/02 8:41 pm
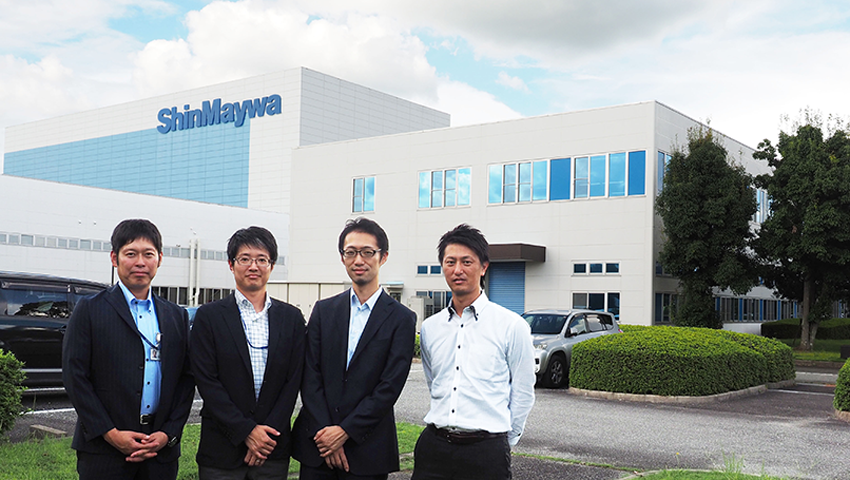
【 Summary 】
ShinMaywa Industries, Ltd. is developing its business as a unified group, from manufacturing to after-sales service, focusing on five fields: aircraft, special purpose vehicles, fluids, industrial machinery systems, and parking systems.
The company’s vision for eliminating labor shortages in maintenance and facility management operations and achieving stable operation through preventive maintenance is to “use IoT to watch over all wastewater treatment facilities,” and the company has introduced a remote monitoring service using the IoT. The company was also using remote monitoring services for its TurboMAX turbo blowers, but the equipment management workload for turbo blowers, including daily management tasks and the preparation of various forms, was too heavy for the company.
To solve the above issues, the company considered introducing a new system because it was found that additional development on the existing system would not be cost-effective. Since the turbo blower remote monitoring service requires the accumulation of a large amount of data, it was assumed that the service would be provided in the cloud, and the ability to customize the service to meet the company’s specifications was also an important factor in the selection process. The service that was selected was IoT Core Connect.
The most important point that they appreciated about IoT Core Connect was its flexibility and scalability, which were commensurate with its cost. The service, based on Microsoft Azure, is a cloud service that can be customized with a dashboard to aggregate necessary information and a graph display screen to monitor driving conditions.
The screen layout of the service was developed to resemble the actual operation panel mounted on a turbo blower, making it possible to check the operation data of the turbo blower without any sense of discomfort. Inspection and maintenance reports were also improved so that they could be output at the touch of a button from the screen in the form of the company’s specifications. In addition, notification e-mails notifying of equipment malfunctions can now include detailed information necessary to identify the cause, which speeds up initial response when maintenance personnel rush to the site and minimizes downtime. The realization of these features is expected to lead to a reduction in the burden of verification work and management costs in the future.
- Category
- System
- Tags
- DXIoTCloudCost savingWork efficiency
- Related URL
- https://www.softbanktech.co.jp/case/list/shinmaywa/
Service provider : | SB Technology Corp. |
---|---|
Service user : | ShinMaywa Industries, Ltd. |
*Check a case study at the related URL on the bottom of this page if the case study is not shown.